Understanding Siemens Product Lifecycle Management
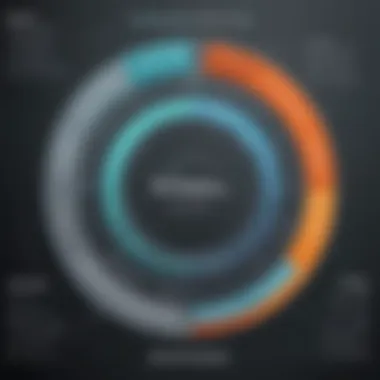
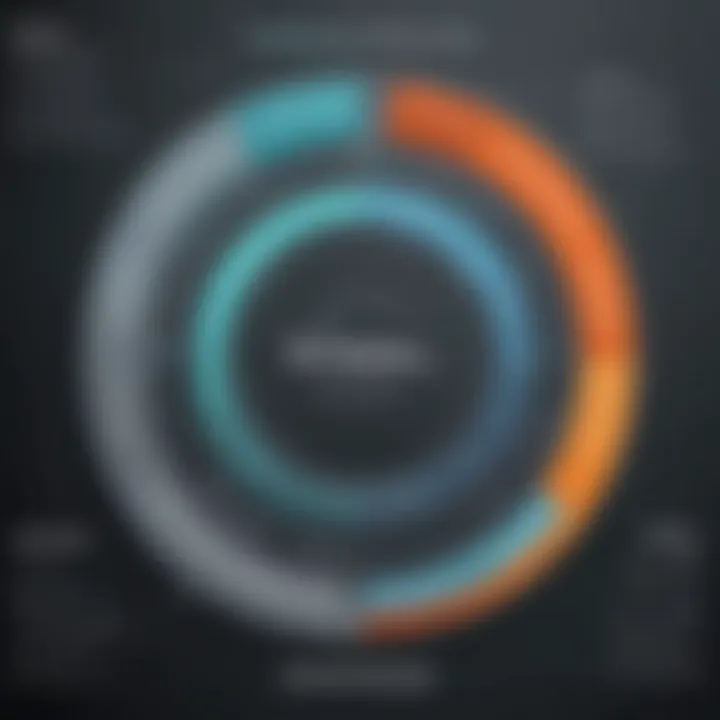
Intro
Siemens Product Lifecycle Management (PLM) system is a comprehensive solution that plays a crucial role in managing a product's journey from its conception to its ultimate disposal. As businesses increasingly face the demands of efficiency and innovation, understanding this system becomes essential. This analysis provides an in-depth view of Siemens PLM, exploring its functionalities, advantages, and applications across varying industries. Through this examination, the article will clarify important processes, key features, and how PLM integrates with other business systems, serving as a vital resource for professionals aiming to enhance their knowledge.
Software Overview
Purpose of the Software
The primary aim of Siemens PLM software is to streamline and optimize the product development process. By enabling businesses to connect insights gained throughout a product's lifecycle, the system improves decision making and efficiency. It allows enterprises to handle vast amounts of data related to design, manufacturing, and distribution effectively. As a result, organizations can quickly adapt to market changes and consumer demands, aligning their strategies with modern business challenges.
Key Features
Siemens PLM encompasses various features that make it a strong tool for businesses. Some of the key characteristics include:
- Data Management: Siemens PLM offers centralized data storage, enabling easy access and management of product information across departments.
- Collaboration Tools: The system supports collaboration among teams, ensuring that design modifications or updates are shared in real-time, enhancing teamwork and project efficiency.
- Process Automation: Automated workflows reduce manual errors and accelerate processes such as approvals and compliance checks.
- Integration Capabilities: Siemens PLM can seamlessly interface with other business applications, ensuring that data flows smoothly throughout the organization.
- Analytics and Reporting: The software provides advanced analytics tools that allow companies to assess product performance and market trends for better strategic decisions.
Comparison with Competitors
Feature-by-Feature Analysis
When comparing Siemens PLM to other solutions on the market, such as PTC Windchill or Dassault Systèmes' ENOVIA, several differences arise. While they may offer similar benefits, Siemens stands out in certain areas:
- User Interface: Many users find Siemens PLM more intuitive and user-friendly compared to competitors.
- Scalability: Siemens PLM offers enhanced scalability options, crucial for small to medium-sized businesses looking to grow.
- Customization: The adaptability of the software allows businesses to customize workflows according to specific needs more easily than with some competitors.
Pricing Comparison
Pricing for Siemens PLM varies depending on the modules selected and the scale of deployment needed for each business. Competitors such as valued PTC Windchill may have different pricing structures. Thus, it is essential for businesses to conduct thorough research and consider their specific requirements when evaluating PLM solutions.
Understanding the unique strengths of Siemens PLM and comparing them against competitors enables businesses to make informed decisions regarding their product lifecycle management strategy.
In summary, Siemens PLM provides robust tools and features that cater to the needs of modern businesses. It helps manage product lifecycles effectively, driving innovation and enabling companies to adapt quickly to changing market demands.
Prologue to Siemens Product Lifecycle Management
The concept of Product Lifecycle Management (PLM) has significant relevance in today's competitive environment. It concerns the systematic management of a product's lifecycle from its inception to eventual retirement. Siemens has created an advanced PLM solution that aids organizations in optimizing their product processes. Understanding the frameworks and functionalities of Siemens PLM is essential for businesses aiming to enhance efficiency and innovation. The focus on PLM is not merely about managing data; it is fundamentally about elevating a company's ability to deliver superior products while reducing time and cost.
Defining Product Lifecycle Management
Product Lifecycle Management refers to the integration of people, processes, and technology to manage a product's lifecycle effectively. This encompasses everything from initial concepts through design, manufacturing, service, and disposal. At the heart of Siemens PLM is the idea that better information leads to better products. By using a PLM system, organizations can keep track of product specifications, changes in design, and other critical factors throughout the lifecycle. This not only fosters collaboration across departments but also ensures that all stakeholders have access to the same updated information, reducing errors and inconsistencies.
Moreover, PLM tools offer powerful insights through data analytics. Companies can understand production trends, customer feedback, and performance data that significantly influence future product development decisions. Thus, Siemens PLM provides a foundation that enables organizations to make informed choices and respond rapidly to market shifts, ultimately leading to enhanced product quality and customer satisfaction.
The Evolution of Siemens PLM
Siemens PLM has undergone substantial evolution over the years, reflecting advancements in technology and shifts in market demands. Initially focused on simple design tools, it has transformed into an intricate ecosystem that supports comprehensive product development. The incorporation of digital technologies changed how products are designed, manufactured, and maintained.
In the early stages, Siemens recognized the need for collaboration among engineering, manufacturing, and service teams. Gradually, they integrated enhanced simulation and modeling tools that allow for real-time data utilization. This shift enabled engineers to predict issues even before the physical prototyping stage. Thus, the evolution of Siemens PLM mirrors the continuous pursuit of operational excellence and competitive advantage against a backdrop of rapid technological advancement.
The development trajectory of Siemens PLM symbolizes not only a response to market needs but also a proactive stance in shaping the future of product development. By staying ahead of trends such as digital twins and smart manufacturing, Siemens PLM continues to provide robust solutions that are vital for today's dynamic business landscape.
Core Components of Siemens PLM
Understanding the core components of Siemens Product Lifecycle Management (PLM) is essential for any business looking to optimize its product development process. These components play a significant role in facilitating efficient data management, enhancing collaboration, and streamlining processes. Together, they combine to create a cohesive system that ensures products are developed and maintained effectively throughout their lifecycle.
Data Management
Data management forms the backbone of Siemens PLM. It involves the collection, storage, and retrieval of product-related data. This is vital as products are developed across different phases and require precise documentation and tracking. Siemens PLM offers robust tools to ensure that every piece of information is organized and accessible. Businesses can manage complex data sets efficiently, maintaining version control and ensuring all stakeholders have access to the latest information.
Proper data management reduces the risk of errors and inconsistencies. With easy access to updated documents, teams can make informed decisions faster. Moreover, it supports regulatory compliance, as companies can store evidence of adherence to industry standards and practices.
Collaboration Tools
Collaboration tools in Siemens PLM enable teams to work together seamlessly, regardless of their location. Effective collaboration is fundamental for project success. With features like real-time updates and shared platforms, team members can communicate openly and address issues as they arise. Siemens PLM connects different departments, ensuring that everyone involved—from engineering to marketing—can share insights and feedback.
These tools help break down silos that often exist in organizations. When teams have access to the same information, they can coordinate actions more effectively, reducing redundancy and improving productivity. Notably, the integration of collaboration features with other systems streamlines workflows and fosters innovation.
Process Management
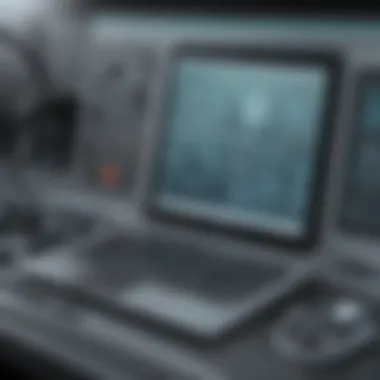
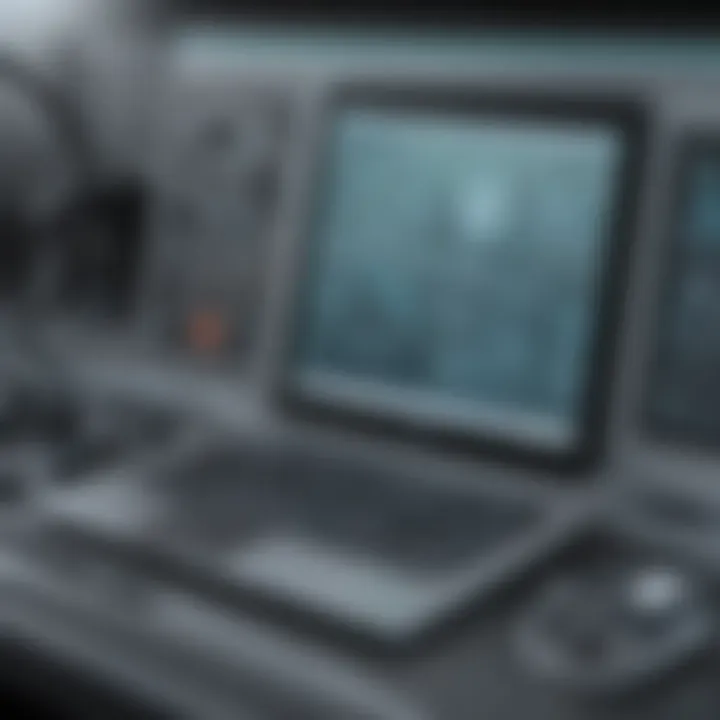
Process management encapsulates the methodologies adopted to oversee the lifecycle of a product within Siemens PLM. Through structured workflows, businesses can define each stage of product development, from conception to retirement. This ensures that every step is followed systematically, which enhances project oversight and minimizes risks.
Siemens PLM allows organizations to establish key performance indicators (KPIs) to monitor progress and success. By analyzing these indicators, businesses can identify bottlenecks or inefficiencies in their processes. As a result, they can implement improvements that lead to better product outcomes and enhanced customer satisfaction.
Additionally, incorporating continuous improvement strategies through process management allows businesses to adapt to market demands swiftly. Companies gain the agility needed to modify designs based on customer feedback or market trends, which is crucial in today’s fast-paced environment.
"The integration of core components in Siemens PLM not only streamlines operations but also enhances strategic decision-making capabilities across various teams."
In summary, the core components of Siemens PLM—data management, collaboration tools, and process management—are integral to a successful product lifecycle strategy. For organizations aiming to leverage these components, understanding their significance is the first step towards enhancing product quality and ensuring organizational efficiency.
Benefits of Implementing Siemens PLM
Implementing Siemens Product Lifecycle Management (PLM) is significant for businesses aiming to streamline processes, enhance product quality, and reduce costs. The benefits gained from this strategic approach can be transformative, especially for small to medium-sized enterprises. As companies face an increasingly competitive landscape, leveraging effective PLM solutions is essential.
Enhanced Product Quality
One of the most pronounced benefits of Siemens PLM is the enhancement of product quality. This system enables organizations to establish structured workflows that ensure thorough quality checks at various stages of the product lifecycle. With advanced tools, companies can identify and rectify flaws early in the development process, preventing costly errors later.
Benefits include:
- Standardization of processes: Siemens PLM encourages adherence to best practices, which leads to more consistent quality across products.
- Real-time data analytics: By analyzing performance metrics, businesses can understand product efficacy and implement changes swiftly.
- Customer feedback incorporation: The system facilitates gathering and utilizing customer insights, enhancing future product designs.
Overall, the focus on quality not only increases customer satisfaction but also strengthens brand reputation.
Cost Reduction Strategies
Implementing Siemens PLM can lead to substantial cost savings. Organizations can streamline operations and identify inefficiencies, ultimately reducing overall expenditures. By adopting a systematic approach to managing product lifecycles, companies can avoid unnecessary expenses associated with product recalls or redesigns.
Key strategies include:
- Minimized waste: Efficient resource management reduces excess materials and associated costs.
- Reduced time on revisions: With an organized framework, teams can address design flaws before they escalate.
- Optimized supply chain: Enhanced visibility allows businesses to negotiate better terms with suppliers and improve inventory turnover.
In summary, Siemens PLM enables organizations to adopt cost-effective practices that contribute to overall financial sustainability.
Improved Time-to-Market
Speed is critical in today’s fast-paced market environment. Siemens PLM significantly accelerates time-to-market, allowing businesses to introduce new products to consumers more promptly. This efficiency stems from streamlined processes and better coordination among different teams throughout the product development lifecycle.
Factors contributing to faster time-to-market include:
- Automated workflows: Automation in repetitive tasks frees up resources for more complex work, expediting development cycles.
- Enhanced collaboration: Teams can work concurrently rather than sequentially, enabling quicker decision-making.
- Proactive problem-solving: Identifying potential delays ahead of time allows teams to address issues before they impact timelines.
In essence, by improving time-to-market, Siemens PLM not only helps businesses stay ahead of competition but also maximizes potential revenue opportunities.
"In today’s economy, being first to market can prove to be the key factor in a product’s success. Efficiency in product development is non-negotiable."
With the right PLM strategy, companies can realize these benefits and achieve a commanding position in their respective markets.
Siemens PLM in Different Industries
Understanding how Siemens Product Lifecycle Management (PLM) can be applied across diverse industries is essential. Each sector has unique challenges and requirements that can be effectively addressed with Siemens PLM solutions. Implementing this system improves efficiencies, drives innovation, and optimizes product quality. Let's explore the application of Siemens PLM in three key industries: Aerospace and Defense, the Automotive Sector, and Consumer Products.
Aerospace and Defense
In the Aerospace and Defense sector, product development is highly complex due to stringent regulations and safety standards. Siemens PLM provides tools for integrated project management and real-time collaboration between teams. With data management capabilities, companies can handle extensive documentation and ensure compliance with safety regulations. This leads to enhanced efficiency in design and reduced risk of non-compliance.
Moreover, features like digital twin technology allow companies to create detailed simulations of products, which can predict performance and identify potential issues early in the development process. The combination of these tools ensures that projects remain on schedule and within budget.
"Effective PLM practices in aerospace can lead to substantial improvements in safety, quality, and cost efficiency."
Automotive Sector
The Automotive Sector has rapidly evolved with the advent of electric vehicles and smart technology integration. Siemens PLM enables automotive manufacturers to manage the lifecycle of their products with a focus on innovation and sustainability. Collaboration tools allow for seamless sharing of information across departments, which helps in expediting the design process. Simultaneously, it reduces possibilities of errors that could come from siloed operations.
Adopting Siemens PLM also helps in lifecycle costing, which focuses on reducing costs not just during manufacturing but throughout the lifespan of the vehicle. This aligns with market demands for affordability and environmental accountability. Through analytics and reporting features, businesses can make informed decisions that align with long-term strategic goals.
Consumer Products
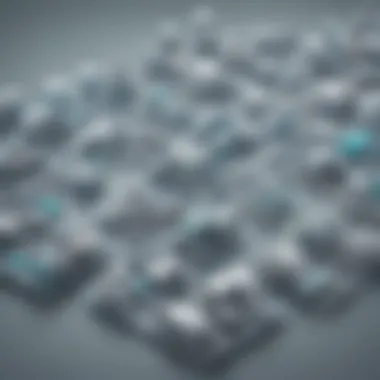
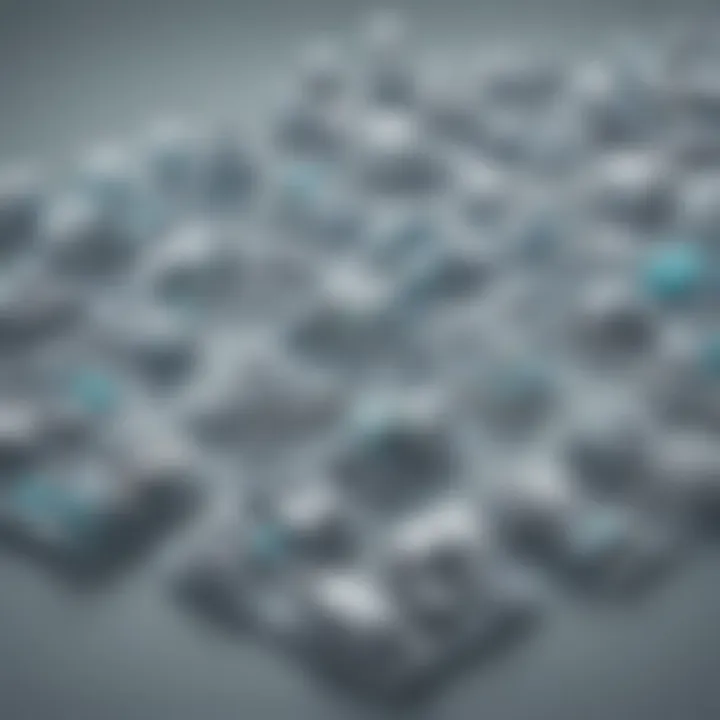
The Consumer Products industry faces the challenge of rapidly changing consumer preferences and fierce competition. To thrive, companies must innovate continuously while also responding to market demands swiftly. Siemens PLM helps address these needs by providing a comprehensive framework for managing product information from concept through retirement.
With the system's robust data analysis tools, organizations can gain insights into consumer trends and product performance. This allows for timely adjustments to designs and marketing strategies, ultimately leading to higher customer satisfaction. Additionally, the platform’s capabilities in supply chain management ensure that products are delivered to market efficiently, maintaining quality while also keeping costs down.
In summary, Siemens PLM plays a crucial role across various industries by enhancing collaboration, improving product quality, and enabling strategic decision-making. By leveraging these advanced tools, businesses can navigate their unique challenges effectively, leading to sustainable growth and competitive advantage.
Integration with Other Business Systems
Integration with other business systems is crucial for a comprehensive Product Lifecycle Management (PLM) strategy. It allows different software systems to communicate and function together smoothly. This integration often impacts the productivity of a business significantly. By connecting Siemens PLM with other essential systems, companies can streamline processes and improve data accuracy. It ensures that information flows seamlessly across departments, reducing the risk of inconsistencies and errors.
A major benefit of this integration is the ability to maintain a single source of truth. With all departments accessing the same data, there is less likelihood of miscommunication. This leads to better decision-making throughout the product lifecycle. Moreover, integration can enhance collaboration across teams. Each team can access relevant data from other departments as needed, fostering a more cooperative environment.
When implementing Siemens PLM, businesses need to consider their existing infrastructures and how new systems will fit. Integrating PLM with other systems often requires a well-thought-out strategy. Factors like cost, compatibility, and employee training are essential to review. Thus, companies may need to allocate resources for initial integration efforts. However, the long-term gains in efficiency usually outweigh these initial investments.
"Effective integration makes PLM a powerful tool in the overall business ecosystem, providing critical advantages in today’s fast-paced market."
ERP Systems
Enterprise Resource Planning (ERP) systems are foundational elements in modern businesses. They centralize an organization’s data and consolidate operations into a cohesive framework. Integrating Siemens PLM with ERP systems enhances the management of financials, supply chains, and human resources.
The synergy between PLM and ERP can lead to improved inventory management. As product designs change, these updates can be reflected automatically in the ERP system. This ensures that manufacturing and supply chains align with the latest product specifications. For small and medium-sized businesses, this can lead to cost savings by avoiding overproduction or wastage. Furthermore, better financial oversight ensures that budgeting aligns with product launches and forecasts.
CAD and Design Tools
Computer-Aided Design (CAD) and design tools play an important role in product development. Integrating Siemens PLM with CAD tools such as SolidWorks or Autodesk can vastly improve the design process. When these systems are connected, data from the design phase is immediately available in the PLM environment.
This integration allows design teams to track changes effectively. Any modifications made to a CAD model can be documented automatically. This ensures that everyone involved is aware of current specifications. Importantly, it reduces delays in product development caused by miscommunication. As a result, projects move from concept to market much more rapidly.
Supply Chain Management
Supply Chain Management (SCM) is another critical area benefiting from Siemens PLM integration. By linking PLM with SCM software, companies can enhance their logistics and tracking capabilities. This integration essentially creates a more agile response to market demands.
For instance, real-time data sharing facilitates better forecasting as supply chain teams can access the latest product insights from PLM. This allows companies to adjust their supply chains according to consumer behavior and production trends. In effect, this speeds up the reaction time to changes in the market, ensuring that businesses can meet customer needs promptly.
Thus, successful integration of Siemens PLM with other business systems is indispensable for higher efficiency, better collaboration, and a smoother workflow.
Best Practices for Implementing Siemens PLM
Implementing Siemens Product Lifecycle Management (PLM) is not merely about technology adoption; it is inherently a strategic undertaking. Best practices play an essential role in securing a successful implementation that aligns with business objectives. These practices help mitigate risks, enhance operational efficiencies, and ensure a smooth transition. The following sections illuminate key aspects that can substantially improve the implementation process of Siemens PLM.
Project Scope Definition
Defining the project scope is a foundational step in the implementation of Siemens PLM. A clear scope statement outlines what will be included, as well as what will be excluded. This clarity helps various stakeholders understand their roles and expectations. Furthermore, a well-defined scope can avert unnecessary expansions that may arise during the implementation process. Critical factors to consider include:
- Identifying Key Objectives: Understand what the business hopes to gain from the PLM system. Be specific in your objectives, whether they involve enhancing data accuracy or improving collaborative tools.
- Resource Allocation: Determine the necessary resources such as human capital, technology requirements, and budget. Having an itemized budget and timeline saves organizations from overrun and unexpected costs.
- Stakeholder Involvement: Engage with all potential users at an early stage. Their insights can assist in tailoring the PLM features to meet specific requirements.
Stakeholder Engagement
Engaging stakeholders is pivotal for the successful adoption of Siemens PLM. The involvement of a wide range of stakeholders—from top management to end-users—fosters a sense of ownership and commitment. Here are some important aspects to focus on for effective stakeholder engagement:
- Communication Channels: Establish clear and open lines of communication. Regular updates inform stakeholders about progress and encourage feedback.
- Collaboration Tools: Utilize tools that facilitate interaction among various stakeholder groups. This could include platforms for project management or shared resources for document review.
- Involvement in Decision Making: Involve key stakeholders in critical decisions regarding PLM features and functionalities. Their input can shape the system's efficacy and relevance to your organization.
User Training and Support
User training and ongoing support are crucial for a successfulPLM implementation. As systems can be complex, providing comprehensive training helps users become proficient quickly. This can minimize errors and improve productivity. Consider the following practices:
- Tailored Training Sessions: Conduct sessions that cater to different user groups based on their roles and needs. For example, engineers might require training on technical specifications while project managers may need focus on data analytics.
- Resource Availability: Develop resources such as manuals, FAQs, and video tutorials that staff can access at any time. This empowers users to learn at their own pace.
- Continuous Support: Establish a support team for addressing user concerns as they search for solutions. A response from knowledgeable personnel can greatly enhance user experience and encourage the adoption of the system.
Successful implementation of Siemens PLM in any organization directly correlates with the attention given to these best practices. Engaging the project scope, stakeholders, and users is integral to fulfilling the PLM's promise of improved product lifecycle management.
Challenges in Siemens PLM Implementation
Implementing Siemens Product Lifecycle Management (PLM) come with significant challenges. Understanding these hurdles is crucial for organizations that wish to fully leverage PLM capabilities. Without addressing these issues, businesses may find the implementation effort lacks effectiveness. The main challenges include: resistance to change, technology adoption issues, and the need for customization. Each of these factors requires careful consideration and strategy to avoid potential pitfalls.
Resistance to Change
Resistance to change is perhaps the most insidious challenge when implementing Siemens PLM. This resistance can stem from various sources within an organization, particularly from employees who feel threatened by new systems. Existing workflows and processes that employees are accustomed to may be disrupted. The emotional response to change can lead to pushback. Therefore, it is of utmost importance to foster a culture of adaptability.
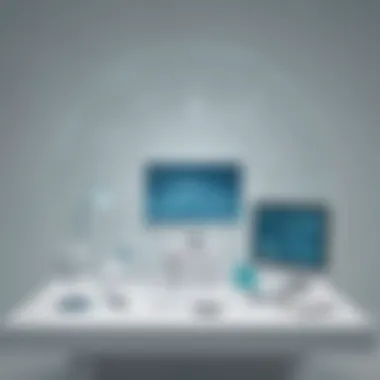
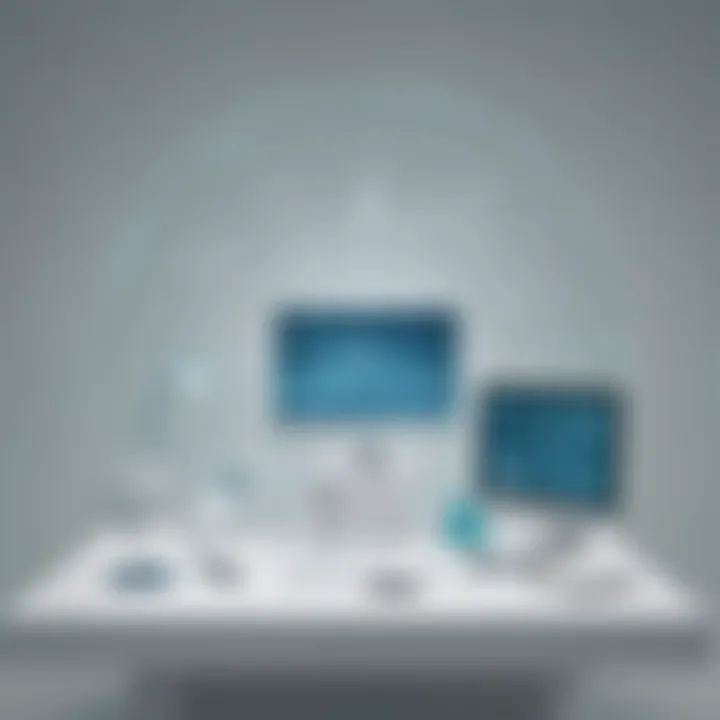
To mitigate this resistance, organizations should:
- Invest in Communication: Clearly articulate the benefits of PLM to all employees.
- Encourage Participation: Involve employees in the planning and design stages of the PLM implementation.
- Provide Support: Offer ongoing support to help employees transition to the new system.
By addressing the human element of the change, companies can smooth the transition process.
Technology Adoption Issues
Adopting new technologies can be a complex endeavor. With Siemens PLM, specific software tools and platforms may require a steep learning curve for users. Insufficient technical training can hinder the effective use of these tools. Furthermore, integration with legacy systems can present additional technical challenges.
To counter these issues, organizations might consider the following:
- Conduct Training Sessions: Comprehensive training programs tailored to different user levels should be implemented.
- Phased Rollouts: Gradually introduce the PLM system rather than a full-scale launch.
- Establish Help Desks: Create support channels where employees can get immediate help with technological challenges.
By ensuring that all users are well-equipped to handle new tools, the risk of failure decreases significantly.
Customization Requirements
Customization is often necessary to ensure that the Siemens PLM system meets specific business needs. However, the process of customizing PLM solutions can be both time-consuming and costly. Too much customization may also lead to complications in system upgrades or maintenance. Companies must strike a balance between customization and standardization.
To effectively manage customization requirements, organizations can:
- Define Clear Objectives: Understand what aspects of the system require customization before starting the process.
- Limit Customization Scope: Focus only on essential areas rather than overhauling the entire system.
- Review Regularly: Establish a continuous review process to assess the effectiveness of custom solutions in place.
Ultimately, this thoughtful approach to customization can lead to a more effective implementation of Siemens PLM, paving the way for successful integration into business operations.
"Navigating challenges is essential to unlocking the full potential of Siemens PLM. Each obstacle offers valuable lessons that can lead to better management of product lifecycles."
In summary, recognizing and addressing these challenges is vital for the successful implementation of Siemens PLM. Failing to do so may lead to wasted resources and unmet expectations.
Future Trends in Product Lifecycle Management
The landscape of Product Lifecycle Management is evolving rapidly. This section delves into the trends that will shape the future of Siemens PLM. By examining Digital Twin Technology, Artificial Intelligence and Machine Learning, and Sustainability in Product Development, we can see how these elements are critical for businesses moving forward.
Digital Twin Technology
Digital Twin Technology refers to the creation of a virtual representation of a physical product or system. This real-time replica helps companies monitor performance and predict issues before they arise. For business, adopting digital twins can lead to:
- Improved Decision Making: With real-time data, organizations can make informed decisions quickly.
- Enhanced Product Development: Companies can simulate various scenarios, reducing the need for physical prototypes.
Digital twins are becoming increasingly vital as businesses seek to improve efficiency and reduce costs. Siemens offers tools that integrate digital twin technology into the product lifecycle, providing a comprehensive view that enables proactive management.
Artificial Intelligence and Machine Learning
Artificial Intelligence and Machine Learning are revolutionizing the PLM industry. These technologies facilitate the processing of vast amounts of data, making it possible to identify trends and insights that human analysts may overlook. Key advantages include:
- Predictive Analytics: AI can predict product performance and market trends, allowing for strategic planning.
- Automation of Processes: Routine tasks can be automated, freeing resources for more complex issues.
Using AI and machine learning within Siemens PLM helps organizations streamline operations and enhance product innovation. The continuous learning aspect of these technologies ensures they evolve alongside market needs, keeping businesses competitive.
Sustainability in Product Development
Sustainability has become an essential consideration in product development. Companies are increasingly aware of the impact of their products on the environment. Implementing sustainable practices in PLM can:
- Reduce Waste: By optimizing resource use, companies can significantly decrease waste during the manufacturing process.
- Meet Regulatory Standards: Companies that adhere to environmental standards avoid penalties and benefit from positive public perception.
Siemens PLM supports these initiatives by offering solutions that integrate sustainability into every phase of a product's lifecycle. This alignment with sustainability not only enhances a company’s reputation but also ensures compliance with evolving regulations.
"The adoption of advanced technologies in PLM will define the competitiveness of businesses in the near future."
As we observe these trends, it is clear that the integration of digital twin technology, artificial intelligence, and sustainability will shape how small to medium-sized businesses manage their product lifecycles. Understanding and implementing these trends will be crucial for their success.
Epilogue
In this part of the article, we emphasize the criticality of effective Product Lifecycle Management (PLM) in today’s fast-paced business environment. The implementation of Siemens PLM offers transformative benefits that help organizations streamline their operations and enhance product quality. Through the insights gained in the previous sections, we have illustrated how Siemens PLM plays a vital role in managing every stage of a product’s lifecycle effectively.
Summary of Key Points
- Critical Components: Siemens PLM encompasses essential components such as data management, collaboration tools, and process management, each underpinning successful product development and deployment.
- Industry Relevance: The application of Siemens PLM spans multiple industries, demonstrating its versatility and ability to cater to diverse business needs. It supports sectors like aerospace, automotive, and consumer products.
- Integration Capabilities: Seamless integration with other business systems, including ERP and CAD tools, maximizes efficiency and ensures consistency across operations.
- Future Trends: Understanding emerging technologies like digital twins and machine learning will be crucial for organizations looking to remain competitive in a rapidly evolving landscape.
Final Thoughts on Siemens PLM Importance
Siemens PLM solutions embody the essence of modern efficiency and innovation. For small to medium-sized businesses, entrepreneurs, and IT professionals, leveraging these solutions is not just an option but a strategic necessity. As markets become increasingly competitive, the ability to manage product lifecycles with agility and precision offers a distinct advantage.
"In the world where products evolve rapidly, effective lifecycle management isn't just beneficial; it's essential for survival."